Opatrenia na zlepšenie kvality výroby v automobilovej spoločnosti
1. | Teoretické východiská zlepšovania kvality |
2. | Opis automobilovej spoločnosti Matador Automotive a.s. |
3. | Opatrenia na zlepšenie kvality výroby v automobilovej spoločnosti
|
Obsah
Cieľom vlastných návrhov a samostatnej práce bude navrhnúť nápravné opatrenia, ktorých úlohou bude zlepšiť úroveň kvality vo firme Matador Automotive, a.s. Tento požadovaný cieľ sa budeme snažiť dosiahnuť prostredníctvom identifikovania oblasti, ktorú firma považuje za kľúčovú, a na ktorú sa budeme musieť pri zlepšovaní kvality zamerať. Túto oblasť následne podrobíme analýze, identifikujeme jej slabé miesta, navrhneme nápravné opatrenia a rozpracujeme. Manažér kvality následne určí, ktoré z opatrení sa budú môcť prakticky aplikovať do prostredia firmy, a ktoré nie. Prijaté opatrenia prakticky zavedieme, vyhodnotíme ich úspešnosť a pokračujeme v trvalom zlepšovaní. Tento postup vychádza z filozofie PDCA cyklu (1.5.1 PDCA cyklus) a prehľadne ho zobrazuje nasledujúci vývojový diagram Obr. 4 Zlepšovanie kvality.
Opis súčasného stavu
V súčasnosti firma musí bojovať nielen proti finančnej kríze, ale musí obstáť aj v každodennom boji s konkurenciou o zákazníka. Firma sa v súčasnosti zameriava na výrobu jednoúčelových strojov a podskupín pre gumárenské stroje, kde spoločnosť zaznamenáva dobré výsledky. Pre uspokojenie nových zákazníkov sa firma začala zameriavať aj na oblasť výroby robotizovaných liniek a lisovacích nástrojov. Na predstavenie Hlavných (kľúčových), Riadiacich a Podporných procesov v spoločnosti nám poslúži nasledujúci obrázok Obr. 5 Mapa procesov.
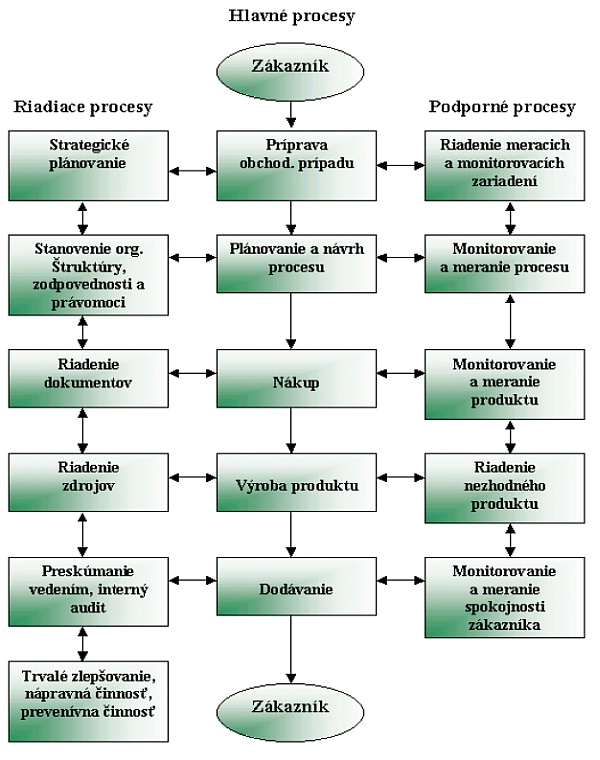
Z predchádzajúceho obrázku vidíme že medzi hlavné (kľúčové) procesy firmy patrí aj proces Výroby produktu. Výroba patrí medzi Alfu a Omegu každej spoločnosti a bez kvalitnej výroby nie je možné úspešne konkurovať okolitému trhu a uspokojovať požiadavky stále náročnejších zákazníkov. Z tohto dôvodu návrh nápravných opatrení na zlepšenie kvality bude smerovať práve na proces Výroby produktu. Samotný proces výroby produktu sa skladá z jednotlivých podprocesov, ktoré nám predstavuje nasledujúci obrázok Obr. 6 Predstavenie procesu výroby produktu.
V ďalšej časti tejto práce sa budeme zameriavať už len na samotný proces Výroby produktu. Pri zlepšovaní kvality v tomto kľúčovom procese sa budeme opierať o filozofiu metódy Kaizen (1.5.2 Kaizen). Metóda pojednáva o tom že ak chceme zlepšiť kvalitu v danom procese, musíme sa zamerať na jeho jednotlivé časti, identifikovať ich slabé miesta a realizovať malé postupné zlepšenia. Túto metódu sme zvolili z toho dôvodu, pretože umožňuje zlepšiť kvalitu v procese výroby prostredníctvom malých nápravných opatrení, ktoré by firme nemali spôsobiť žiadne veľké finančné zaťaženie. Tým pádom bude splnená požiadavka spoločnosti Matador Automotive a.s. , ktorú kladie na túto diplomovú prácu – maximálny zisk, minimálne náklady.
Monitorovanie a meranie
V predchádzajúcej časti tejto práce sme určili, že oblasťou na ktorú sa máme pri zlepšovaní kvality zamerať je proces Výroba produktu. Teraz je veľmi dôležité stanoviť relevantné ukazovatele, ktoré budeme monitorovať a analyzovať. Ukazovatele by mali byť jednoduché, pochopiteľné a mali by disponovať s výpovednou funkciou. Z tohto dôvodu boli za relevantné ukazovatele stanovené počet výskytu nezhodných produktov a náklady na nezhodné produkty. Monitorovaným obdobím sú roky 2006 až 2009.
Prehľad výskytu nezhodných produktov za roky 2006 až 2009.
Obdobie rokov 2006 až 2009 | ||||
---|---|---|---|---|
2006 | 2007 | 2008 | 2009 | |
Počet nepodarkov (ks) | 14 | 23 | 17 | 30 |
Porovnanie nákladov na nezhodné produkty za roky 2006 až 2009
Obdobie rokov 2006 až 2009 | ||||
---|---|---|---|---|
2006 | 2007 | 2008 | 2009 | |
Náklady na nepodarky (?) | 3 104,49 | 5 070,01 | 3 460,67 | 5 931,32 |
Prehľad výskytu nezhodných produktov a nákladov pre jednotlivé podprocesy výroby za roky 2006 až 2009
V procese výroby produktu sledujeme deväť jednotlivých podprocesov (Zváranie, Zámočnícke práce, Brúsenie, Frézovanie, Sústružnícke práce, Horizontovanie, NC a CNC, Natieranie, Pieskovanie). Nasledujúca Tab.3 nám vyjadruje počet nezhodných produktov a nákladov, ktoré vznikli v jednotlivých podprocesoch za sledované obdobie rokov 2006 až 2009.
Podproces | Náklady (?) | Počet nezhod. produktov (ks) | ||||||
---|---|---|---|---|---|---|---|---|
2006 | 2007 | 2008 | 2009 | 2006 | 2007 | 2008 | 2009 | |
Zváranie | 50.62 | 656.87 | 26.19 | 78.04 | 2 | 2 | 1 | 1 |
NC a CNC | 903.84 | 1746.27 | 863.51 | 3486.19 | 3 | 2 | 4 | 9 |
Zámočnícke práce | 276.80 | 1175.40 | 423.39 | 143.70 | 1 | 4 | 2 | 6 |
Frézovanie | 40.80 | 16.60 | 845.05 | 334.26 | 1 | 1 | 3 | 2 |
Sústružnícke práce | 44.05 | 173.50 | 69.71 | 210.62 | 1 | 2 | 1 | 1 |
Horizontovanie | 316.94 | 816.57 | 530.90 | 143.40 | 2 | 4 | 3 | 1 |
Brúsenie | 999.80 | 149.37 | 519.05 | 829.18 | 3 | 5 | 1 | 5 |
Natieranie | 0.00 | 21.58 | 106.35 | 56.43 | 0 | 1 | 1 | 1 |
Pieskovanie | 471.65 | 313.85 | 76.51 | 649.51 | 1 | 2 | 1 | 4 |
Spolu | 3104.49 | 5070.01 | 3460.67 | 5931.32 | 14 | 23 | 17 | 30 |
Analýza dát
Cieľom tejto časti práce je vyhodnotenie monitorovaných ukazovateľov za sledované obdobie rokov 2006 až 2009. Prvoradou úlohou bude určenie tých najslabších miest (najslabších podprocesov) výroby produktu, pretože práve tam by mali smerovať prvé nápravné opatrenia. Identifikovanie tých podprocesov, ktoré svojou činnosťou najviac zaťažili tvorbu nákladov na nezhodnú výrobu a následné zameranie sa na tieto podprocesy, bude tým najlepším riešením za účelom zníženia nákladov, vyplývajúcich z neželanej nezhodnej výroby. K tomuto účelu využijeme Paretovú analýzu (1.5.3 Paretová analýza).
Z grafu Paretovej analýzy pre ukazovateľ výskytu nepodarkov vyplýva, že pri návrhu nápravných opatrení sa musíme najskôr zamerať na podprocesy: NC a CNC, Brúsenie, Zámočnícke práce, Horizontovanie, Pieskovanie, Frézovanie.
Z grafu Paretovej analýzy pre ukazovateľ náklady na nepodarky vyplýva, že pri návrhu nápravných opatrení sa musíme najskôr zamerať na podprocesy: NC a CNC, Brúsenie, Zámočnícke práce, Horizontovanie.
V ďalšej časti tejto práce sa budeme opierať o výsledky Paretovej analýzy pre ukazovateľ nákladov na nepodarky. Tento ukazovateľ sme si zvolili za relevantnejší z toho dôvodu, pretože zamerať sa na podprocesy, ktoré sa svojou činnosťou najviac podieľali na tvorbe nákladov, bude tým najefektívnejším riešením za účelom zníženia nákladov vyplývajúcich z nezhodnej výroby.
Aplikácia nástrojov manažérstva kvality
Cieľom tejto časti práce bude za pomoci aplikácie manažérskych nástrojov identifikovať pre každý sledovaný podproces výroby (NC a CNC, Brúsenie, Zámočnícke práce, Horizontovanie) príčiny, ktoré viedli k vzniku nezhodných produkov a určiť tie najzávažnejšie na ktoré sa budeme musieť zamerať. K tomuto účelu využijeme nástroje Brainstorming (1.5.4 Brainstorming), Ishikawov diagram (1.5.5 Ishikawov diagram) a Paretovú analýzu (1.5.3 Paretová analýza).
Metódu Brainstormingu využijeme za účelom zostavenia Ishikawovho diagramu, kde zamestnanci sledovaných podprocesov na základe svojich vedomostí a skúseností predstavia všetky príčiny, aké môžu viesť k vzniku nezhodných produktov v piatich skupinách: Ľudia, Materiál, Zariadenie, Metódy, Okolie. Očakávaným úžitkom zostaveného Ishikawovho diagramu bude všeobecné predstavenie všetkých možných príčin, a identifikovanie aj takých príčin o akých sa doteraz vôbec ani neuvažovalo.
Metódu Paretovej analýzy využijeme pri posudzovaní záznamov systému manažérstva kvality o výskyte nepodarkov. Tieto záznamy budeme musieť analyzovať za účelom zistenia konkrétnych relevantných príčin, ktoré viedli k vzniku nezhodných produktov. Úlohou Paretovej analýzy bude identifikovanie tých príčin, na ktorých odstránenie sa budeme musieť najskôr zamerať. Relevantnými dokumentami budú záznamy o výskyte nepodarkov za roky 2006 až 2009. Kľúčovým ukazovateľom budú opäť náklady na nepodarky.
Analýza podprocesu NC a CNC
Realizácia brainstormingu
Podrobné informácie ako bol uskutočnený brainstorming s pracovníkmi podprocesu NC a CNC predstavuje nasledujúca tabuľka Tab. 6. Rovnakým spôsobom, teda tabuľkovou formou predstavíme uskutočnené brainstormingi aj pre ostatné sledované podprocesy výroby produktu. Spoločnou črtou všetkých zrealizovaných brainstormingov je téma, miesto uskutočnenia a moderátor. Ostatné faktory sú pre každý podproces rozdielne.
Téma brainstormingu | Miesto, dátum a čas uskutočnenia | Počet zúčastnených pracovníkov | Identifikácia zúčastnených pracovníkov | Moderátor brainstormingu |
---|---|---|---|---|
Identifikácia príčin vzniku nezhodného produktu | Dubnica nad Váhom, 13.12.2009, 11:00-11:20 | 7 | Operátori NC a CNC zariadení | Riešiteľ DP (Pre ďalšie realizácie brainstormingu bude najvhodnejším moderátorom Vedúci podprocesu NC a CNC) |
Zostavenie Ishikawovho diagramu
Na základe výsledkov brainstormingu pre podproces NC a CNC sme zostavili nasledujúci Ishikawov diagram Obr. 9, kde sú v piatich skupinách predstavené všetky relevantné príčiny, ktoré môžu viesť k vzniku nezhodného produktu.
Analýza záznamov o nezhodách
Por. číslo | Názov nezhodnej položky | Počet nezhôd (ks) | Počet celkovo vyrob. (ks) | Náklady na nezhody (?) | Popis nezhody | ||
---|---|---|---|---|---|---|---|
Označenie | Príčina | Zodpovedný | |||||
1. | MP4-002273/ HRIADEL | 3 | 3 | 2980,00 | Chyba v TP | Technológ mal dať zhotoviť dieru na ?10H7 a napísal ?10 | Technológ |
2. | MP4-0021 /HRIADEL | 5 | 5 | 2525,20 | Chyba v TP | Technológ mal dať zhotoviť závit M10 a zadal vŕtať na ?10 | Technológ |
3. | O-KRUZOK 355x5 NBR | 2 | 50 | 543,10 | Chyba materiálu | Pri sústružení sa v materiály objavili vmesky (kazy) | Nákup materiálu |
4. | TF 12984 / ASTA | 2 | 2 | 438,00 | Chyba v TP | Technológ nezadal pridanie prídavku na kalenie a cementovanie | Technológ |
5. | KA-1101-18A 3/1/ VALEC | 2 | 84 | 347,30 | Chyba zvárania | Pri predvýrob. zváraní podskupín nebol dodržaný TP čo spôsobilo následne zlé sústružnícke opracovanie | Pracovník podprocesu zváranie |
6. | M-25400 / GESTELL RI | 4 | 4 | 166,21 | Chyba v tepelnom spracovaní | Materiál nemal predpísané chemické vlastnosti pretože namiesto žíhania pri 2000C bol žíhaný pri 1100C | Oddelenie Kooperácie |
Spolu | 18 | 148 | 6999,81 |
Predchádzajúca tabuľka Tab. 7 predstavuje, aké nezhodné produkty sa za sledované obdobie rokov 2006 až 2009 v podprocese NC a CNC vyskytli. Rovnakú tabuľku použijeme aj u ostatných sledovaných podprocesov za účelom analýzy nezhodnej výroby.
Určenie dominantných príčin
Z grafu Paretovej analýzy pre podproces NC a CNC vyplýva, že príčiny na ktoré sa budeme musieť zamerať sú:
- Technológ mal dať zhotoviť dieru na ?10H7 a napísal ?10,
- Technológ mal dať zhotoviť závit M10 a zadal vŕtať na ?10.
Tieto chyby však nespôsobili pracovníci podprocesu NC a CNC, ale pracovníci oddelenia Technológia, ktorý tým že uvoľnili do výroby nekvalitný technologický postup, zapríčinili vznik nezhodného produktu v podprocese NC a CNC. Z tohto dôvodu pri návrhu nápravných opatrení sa budeme musieť v prvom rade zamerať na oddelenie Technológia.
Ďalšou veľmi dôležitou skutočnosťou je fakt, že nekvalitný technologický postup zapríčinil vyrobenie celej série nekvalitne. Z toho dôvodu ďalší návrh nápravných opatrení bude smerovať aj do podprocesu NC a CNC, kde sa budeme snažiť navrhnúť, také nápravné opatrenia, ktoré by prípadnú nezhodu dokázali okamžite identifikovať (napr. hneď po vyrobení prvého kusu) a nedovolili by vyrobiť celú sériu nekvalitne.
Nástroj Paretovej analýzy použijeme aj u ostatných sledovaných podprocesov, za účelom identifikácie relevantných príčin, na ktorých odstránenie sa budeme musieť zamerať.
Analýza podprocesu Brúsenie
Realizácia brainstormingu
Téma brainstormingu | Miesto, dátum a čas uskutočnenia | Počet zúčastnených pracovníkov | Identifikácia zúčastnených pracovníkov | Moderátor brainstormingu |
---|---|---|---|---|
Identifikácia príčin vzniku nezhodného produktu | Dubnica nad Váhom, 13.12.2009, 11:00-11:20 | 5 | Vedúci dielne, Operátori brúsnych zariadení | Riešiteľ DP (Pre ďalšie realizácie brainstormingu bude najvhodnejším moderátorom Vedúci podprocesu Brúsenie) |
Zostavenie Ishikawovho diagramu
Analýza záznamov o nezhodách
Por. číslo | Názov nezhodnej položky | Počet nezhôd (ks) | Počet celkovo vyrob. (ks) | Náklady na nezhody (?) | Popis nezhody | ||
---|---|---|---|---|---|---|---|
Označenie | Príčina | Zodpovedný | |||||
1. | LA-455B DOSKA DOLNÁ | 3 | 3 | 642,30 | Chyba v zlom výbere kotúča | Pracovník nepoužil kotúč, aký bol predpísaný podľa TP | Pracovník oddelenia Brúsenie |
2. | LA-408A DOSKA DOLNÁ | 2 | 17 | 507,90 | Chyba v zlom nastavení | Podľa chybne nastaveného mikrometra bolo nastavené meradlo Supito | Pracovník oddelenia Brúsenie |
3. | JUS-004 / NAST BLOK | 3 | 10 | 470,10 | Chyba v zlom nastavení | Chybne nastavený mikrometer viedol k nesprávnemu úberu materiálu | Pracovník oddelenia Brúsenie |
4. | SKRINKA SL03 | 2 | 2 | 240,00 | Chyba v zlom výbere kotúča | Podľa TP mal byť použitý leštiaci kotúč na hotovo, ale pracovník použil hrubozrnný kotúč | Pracovník oddelenia Brúsenie |
5. | 06-0291 / SKRINA | 1 | 1 | 221,60 | Chyba v zlom výbere kotúča | Pracovník nepoužil kotúč, aký bol predpísaný podľa TP | Pracovník oddelenia Brúsenie |
6. | PZ3 / HLAVA | 1 | 41 | 196,00 | Chyba zariadenia | Zlyhanie hydrauliky spôsobilo poškodenie kotúča a materiálu | Zariadenie |
7. | 43 DIELEC BVPA | 1 | 26 | 132,50 | Chyba v zlom nastavení | Chybne nastavený mikrometer viedol k nesprávnemu úberu materiálu | Pracovník oddelenia Brúsenie |
8. | JUS-005/ NAST BLOK | 1 | 9 | 87,00 | Chyba v zlom nastavení | Podľa chybne nastaveného mikrometra bolo nastavené meradlo Supito | Pracovník oddelenia Brúsenie |
Spolu | 14 | 109 | 2497,40 |
Určenie dominantných príčin
Z grafu Paretovej analýzy pre podproces Brúsenie vyplýva že príčinami na ktoré sa budeme musieť zamerať sú:
- Pracovník nepoužil kotúč, aký bol predpísaný podľa TP,
- Podľa chybne nastaveného mikrometra bolo nastavené meradlo Supito,
- Chybne nastavený mikrometer viedol k nesprávnemu úberu materiálu,
- Podľa TP mal byť použitý leštiaci kotúč na hotovo, ale pracovník použil hrubozrnný kotúč.
Spoločnou črtou všetkých relevantných príčin, na ktorých odstránenie sa musíme zamerať je ľudský faktor. Vo všetkých prípadoch figuruje ľudská chyba ako prvotná príčina. Z toho dôvodu návrh nápravných opatrení by sa mal uberať takým smerom, a k takým metódam, ktoré zabraňujú pracovníkovi vykonanie chyby pri práci.
Analýza podprocesu Zámočnícke práce
Realizácia brainstormingu
Téma brainstormingu | Miesto, dátum a čas uskutočnenia | Počet zúčastnených pracovníkov | Identifikácia zúčastnených pracovníkov | Moderátor brainstormingu |
---|---|---|---|---|
Identifikácia príčin vzniku nezhodného produktu | Dubnica nad Váhom, 14.12.2009, 11:00-11:20 | 5 | Vedúci dielne, Operátori zámočníckej dielne | Riešiteľ DP (Pre ďalšie realizácie brainstormingu bude najvhodnejším moderátorom Vedúci podprocesu Zámočnícke práce) |
Zostavenie Ishikawovho diagramu
Analýza záznamov o nezhodách
Por. číslo | Názov nezhodnej položky | Počet nezhôd (ks) | Počet celkovo vyrob. (ks) | Náklady na nezhody (?) | Popis nezhody | ||
---|---|---|---|---|---|---|---|
Označenie | Príčina | Zodpovedný | |||||
1. | MR.63A ELESA+GANTNER | 5 | 5 | 890.50 | Chyba spôsobená použitím zle označ. nástroja | Pracovník použil zle označený výstružník, mala byť vystrúžená diera na ? 6H7 a bola vystrúžená na ? 6H11 | Pracovné prostredie |
2. | A3 05 105/ EXZENTERHUELSE | 4 | 4 | 660.59 | Chyba z použitia nespráv. nástroja | Podľa TP mala byť zhotovená diera na ?5H8, ale pracovník namiesto predvŕtania s vrtákom ?4,75 a nasledne výstružníkom ?5H7 vŕtal hneď s vrtákom ?5 | Pracovník oddelenia Zámočnícke práce |
3. | MP2 / SEGMENT I.MPM | 2 | 34 | 220.60 | Chyba v zlom zameraní | Pracovník zle nameral vzájomné vzdialenosti (rozteč)čo spôsobilo zlé navŕtanie dier | Pracovník oddelenia Zámočnícke práce |
4. | PZ3 RAMENO h12 | 1 | 1 | 127.30 | Chyba spôsobená použitím zle označ. nástroja | Pracovník použil zle ozančený vrták namiesto ?8 vŕtal vrtákom ?8,2 | Pracovné prostredie |
5. | 708/ BU LINKS | 1 | 1 | 120.30 | Chyba v nedodržaní TP | V TP bolo napísané vŕtať s vrtákom?8 a pracovník vŕtal s vrtákom ?10 | Pracovník oddelenia Zámočnícke práce |
Spolu | 13 | 45 | 2019.29 |
Určenie dominantných príčin
Z grafu Paretovej analýzy pre podproces Zámočnícke práce vyplýva že príčinami na ktoré sa budeme musieť zamerať sú:
- Pracovník použil zle označený výstružník, mala byť vystružená diera na ? 6H7 a bola vystružená na ? 6H11,
- Podľa TP mala byť zhotovená diera na ?5H8, ale pracovník namiesto predvŕtania s vrtákom ?4,75 a následne výstružníkom ?5H7 vŕtal hneď s vrtákom ?5.
Paretova analýza určila, že relevantné príčiny, na ktorých odstránenie sa máme zamerať sú spôsobené pracovným prostredím (usporiadaním, označením nástrojov) a ľudským faktorom. Z toho dôvodu pri návrhu nápravných opatrní budeme musieť aplikovať metódy, ktoré riešia pracovné prostredie a zaoberajú sa ľudským faktorom (problematiku ľudského faktoru riešime aj v podprocese Brúsenie).
Analýza podprocesu Horizontovanie
Realizácia brainstormingu
Téma brainstormingu | Miesto, dátum a čas uskutočnenia | Počet zúčastnených pracovníkov | Identifikácia zúčastnených pracovníkov | Moderátor brainstormingu |
---|---|---|---|---|
Identifikácia príčin vzniku nezhodného produktu | Dubnica nad Váhom, 14.12.2009, 10:30-10:50 | 9 | Operátori horizontálnych zariadení | Riešiteľ DP (Pre ďalšie realizácie brainstormingu bude najvhodnejším moderátorom Vedúci podprocesu Horizontovanie) |
Zostavenie Ishikawovho diagramu
Analýza záznamov o nezhodách
Por. číslo | Názov nezhodnej položky | Počet nezhôd (ks) | Počet celkovo vyrob. (ks) | Náklady na nezhody (?) | Popis nezhody | ||
---|---|---|---|---|---|---|---|
Označenie | Príčina | Zodpovedný | |||||
1. | PRETLAK KOCKA KL5 | 2 | 5 | 543.20 | Chyba v uhľovaní stroja | Zlé uhľovanie vretena spôsobilo navŕtanie diery pod zlým uhlom | Zariadenie |
2. | OKRUZOK 146NBR-70 | 2 | 20 | 477.10 | Chyba z opotreb. stroja | Vreteno na horizontke malo vôľu v ložiskách čo spôsobilo nedodržanie kruhovitosti | Zariadenie |
3. | PRETLAKKOCKA KL5 | 1 | 12 | 250.90 | Chyba v uhľovaní stroja | Zlé uhľovanie vretena spôsobilo navŕtanie diery pod zlým uhlom | Zariadenie |
4. | TORLEX 447-TA | 1 | 1 | 190.50 | Chyba v nedodržaní TP | Nedodržanie TP, mala sa spraviť diera ?20H7, ale pracovník namiesto použitia vrtáka ?19,75 a potom výstružníka vŕtal hneď vrtákom ?20 | Pracovník oddelenia Horizontov. |
5. | GRUELL P4-3816 | 1 | 27 | 150.20 | Chyba z poškod. nástroja | Pri opracovaní sa nástroj vylúpil a poškodil polotovar. | Zariadenie |
6. | 92 / MADREVITE SX | 1 | 8 | 90.00 | Chyba zlého nastavenia | Navŕtanie dier mimo stred osi, vplyvom zlého vyrovnania výrobku | Pracovník oddelenia Horizontov. |
7. | ROMEL VXP | 1 | 1 | 77.31 | Chyba v TP | Technológ mal dať zhotoviť dieru na ?10H7, ale predpísal len ?10 | Technológ |
8. | GRUELL P5BX | 1 | 130 | 28.60 | Chyba z nespráv. chladenia stroja | Pred sústružením nebola skontrolovaná chladiaca emulzia, pri opracovaní diery sa následne zadrel výstružník | Pracovník oddelenia Horizontov. |
Spolu | 10 | 204 | 1807.81 |
Určenie dominantných príčin
Z grafu Paretovej analýzy pre podproces Horizontovanie vyplýva že príčinami na ktoré sa budeme musieť zamerať sú:
- Zlé uhľovanie vretena spôsobilo navŕtanie diery pod zlým uhlom,
- Vreteno na horizontke malo vôľu v ložiskách, čo spôsobilo nedodržanie kruhovitosti,
- Nedodržanie TP, mala sa spraviť diera ?20H7, ale pracovník namiesto použitia vrtáka ?19,75 a potom výstružníka vŕtal hneď vrtákom ?20.
Na základe výsledkov paretovej analýzy môžeme povedať, že relevantné príčiny na ktorých odstránenie sa máme zamerať, boli spôsobené chybou zariadenia a chybou vyplývajúcou z ľudského faktora. Z toho dôvodu pri návrhu nápravných opatrení budeme musieť vychádzať z takých metód a postupov, ktoré riešia nekvalitu spôsobenú technickým zariadením a nekvalitu spôsobenú ľudským faktorom (problematiku ľudského faktora už riešime, a to v podprocese Zámočnícke práce a Brúsenie).
Návrh nápravných opatrení
Cieľom nápravných opatrení bude zníženie tvorby nákladov na nezhodné výrobky pri dodržaní stanovenej podmienky, ktorú firma kladie na túto diplomovú prácu: maximálny zisk, minimálne náklady. Pri návrhu nápravných opatrení budeme vychádzať z výsledkov predchádzajúcej časti tejto práce 3.4 Aplikácia nástrojov manažérstva kvality, kde sme určili na aké relevantné príčiny, sa máme pri návrhu nápravných opatrení zamerať.
Návrh pre oddelenie Technológia a podproces NC a CNC
Nasledujúca tabuľka Tab. 18 vyjadruje navrhované nápravné opatrenia, ktoré by sa mali prakticky aplikovať do prostredia firmy. Tieto návrhy teraz rozpracujeme do podoby v akej budú prezentované manažérovi kvality, ktorý následne rozhodne či sa budú môcť prakticky aplikovať, alebo nie. Rovnaký postup využijeme aj pre ostatné sledované podprocesy.
Príčina nezhody | Navrhované nápravné opatrenie |
---|---|
Technológ mal dať zhotoviť dieruna ?10H7 a napísal ?10 | Zavedenie štatistickej prebierky |
Technológ mal dať zhotoviť závit M10 a zadal vŕtať na ?10 | Zavedenie štatistickej prebierky |
Zavedenie štatistickej prebierky do oddelenia Technológia
- Zodpovedný pracovník
- Vedúci oddelenia Technológia
- Popis nápravného opatrenia
- Navrhované nápravné opatrenie vychádza z filozofie Štatistickej prebierky (1.5.6 Štatistická prebierka), ktorej úlohou je na základe preberacieho pravidla určiť či bude produkt prijatý, alebo nie. Štatistická prebierka zabraňuje tomu, aby sa do výrobného procesu nedostali produkty, ktoré nespĺňajú požadovanú kvalitu, v našom prípade je produktom technologický postup. Na základe tejto filozofie pracovník oddelenia Technológia, keď vypracuje technologický postup príde za vedúcim oddelenia, ktorý na základe preberacieho pravidla vyberie náhodne desať výrobných operácií, ktoré si sám prekontroluje. V prípade veľkej pracovnej vyťaženosti vedúci oddelenia môže túto úlohu delegovať na jedného zo svojich podriadených. Podmienkou bude, že túto kontrolu nesmie vykonať pracovník, ktorý daný technologický postup vyhotovil. Dôvod je jednoduchý, keďže pracovníci zvyčajne svoje vlastné chyby odhaliť nedokážu. Ak sa pri kontrole zistí, že jedna z desiatich kontrolovaných výrobných operácií je chybná, znamená to že technologický postup vyhovuje na 90%, čo je už neprijateľná hodnota, keďže technologický postup musí vyhovovať na plných 100%. V tom prípade sa technologický postup vráti späť svojmu zhotoviteľovi na opätovné komplexné prekontrolovanie, keďže je predpoklad, že sa v ňom môžu nachádzať ďalšie chyby. Vedúci oddelenia, ale aj jednotlivý technológovia si musia uvedomiť zodpovednosť za svoju prácu, keďže uvoľnenie nekvalitného technologického postupu znamená následne vznik nezhodného produktu.
- Očakávania od nápravného opatrenia
- Navrhované nápravné opatrenie by malo zabrániť chybnému technologickému postupu dostať sa do výrobného procesu, a tým spôsobiť vznik nezhodných výrobkov. Výhodou nápravného opatrenia sú jeho minimálne náklady na zavedenie.
Zavedenie štatistickej prebierky do podprocesu NC a CNC
- Zodpovedný pracovník
- Vedúci oddelenia Riadenie kvality
- Popis nápravného opatrenia
- Navrhované nápravné opatrenie vychádza opäť, z filozofie Štatistickej prebierky (1.5.6 Štatistická prebierka), ktorej úlohou je na základe preberacieho pravidla určiť či bude produkt prijatý, alebo nie. Úlohou štatistickej prebierky bude v tomto prípade zabrániť tomu, aby nebola celá séria vyrobená nezhodne. Princíp spočíva v tom, že pracovníci oddelenia Riadenie kvality na základe preberacieho plánu, budú aktívne monitorovať výrobu v podprocese NC a CNC. Podstatou včasnej identifikácie nezhody bude jej okamžité odstránenie a zabránenie, aby sa prejavila aj u ostatných ešte nevyrobených kusoch. Pri tejto práci budú pracovníci oddelenia Riadenie kvality postupovať podľa nasledujúcich kritérií.
- Kritéria preberacieho plánu
Kritérium č.1 – ak sa bude jednať o drahý výrobok s malou početnosťou, uplatnia sa nasledovné kontrolné kritériá:
Počet vyrobených kusov | Určenie, ktoré kusy sa budú kontrolovať |
---|---|
1 až 5 | Kus číslo: 1, 3, 5 |
6 až 10 | Kus číslo: 2, 4, 6, 8 |
11 až 15 | Kus číslo: 3, 6, 9, 12, 15 |
Kritérium č.2 – ak sa bude jednať o drahý výrobok s veľkou početnosťou, uplatnia sa nasledovné kontrolné kritériá:
Počet vyrobených kusov | Určenie, ktoré kusy sa budú kontrolovať |
---|---|
16 až 25 | Kus číslo: 5, 10, 15, 20, 25 |
26 až 45 | Kus číslo: 6, 12, 18, 24, 30, 36, 42 |
46 až 65 | Kus číslo: 9, 18, 27, 36, 45, 54, 63 |
66 až 85 | Kus číslo: 12, 24, 36, 48, 60, 72, 84 |
nad 85 | Každý dvadsiaty kus |
Kritérium č.3 – ak sa bude jednať o lacnejšie výrobky s malou početnosťou, uplatnia sa nasledovné kontrolné kritériá:
Počet vyrobených kusov | Určenie, ktoré kusy sa budú kontrolovať |
---|---|
1 až 5 | Kus číslo: 3 |
6 až 10 | Kus číslo: 4, 8 |
11 až 15 | Kus číslo: 7, 14 |
Kritérium č.4 – ak sa bude jednať o lacnejšie výrobky s veľkou početnosťou, uplatnia sa nasledovné kontrolné kritériá:
Počet vyrobených kusov | Určenie, ktoré kusy sa budú kontrolovať |
---|---|
16 až 25 | Kus číslo: 8, 16, 24 |
26 až 45 | Kus číslo: 15, 30, 45 |
46 až 65 | Kus číslo: 16, 32, 48, 64 |
66 až 85 | Kus číslo: 21, 42, 63, 84 |
nad 85 | Každý tridsiaty kus |
Preberací plán:
- ↑ Príručka kvality 2010. Dubnica nad Váhom: Matador Automotive a.s., 2010. 29 s.