Návrh súboru opatrení na zlepšenie kvality výroby v danej automobilovej spoločnosti
![]() |
Trenčianska Univerzita Alexandra Dubčeka v Trenčíne
Fakulta Mechatroniky |
![]() |
Návrh súboru opatrení na zlepšenie kvality výroby v danej automobilovej spoločnosti Diplomová práca |
Autor: | Bc. Roman Minárech |
Pedagogický vedúci: |
doc. Ing. Peter Ponický, PhD. |
Študijný odbor: | Manažérstvo kvality produkcie
|
Akademický rok |
2009/2010
|
1. | Teoretické východiská zlepšovania kvality |
2. | Opis automobilovej spoločnosti Matador Automotive a.s. |
3. | Opatrenia na zlepšenie kvality výroby v automobilovej spoločnosti
|
Obsah
Abstrakt
Táto diplomová práca sa zaoberá zlepšovaním systému manažérstva kvality vo firme, ktorá je certifikovaná normou STN EN ISO 9001:2001. Vybranou spoločnosťou je Matador Automotive, a.s. Dubnica nad Váhom. Cieľom tejto práce je navrhnúť nápravné opatrenia, ktoré by sa mohli prakticky aplikovať do prostredia firmy, za účelom zlepšenia kvality výroby. Diplomová práca obsahuje teoretické východiská, ktoré slúžia ako zdroj pre ďalšie praktické časti práce. Predstavené teoretické východiská sa zameriavajú na proces zlepšovania kvality, spôsoby, zdroje, postupnosti a nástroje, ktoré sa využívajú za účelom riadenia a zlepšovania kvality. V práci sa tiež popisuje predmet podnikania a ďalšie dôležité informácie ohľadom vybranej spoločnosti Matador Automotive, a.s. Samotný proces zlepšovania kvality sa realizuje prostredníctvom vývojového diagramu, ktorý predstavuje sled jednotlivých činností, ktoré sa za účelom zlepšenia kvality musia uskutočniť. Tieto etapy sa následne v diplomovej práci podrobne prakticky rozpracujú. Pri ich vypracovávaní sa vychádza už z predstavených teoretických východísk. Za pomoci kombinácie viacerých manažérskych nástrojov sa navrhnú konkrétne nápravné opatrenia, ktorých cieľom je zlepšiť kvalitu výroby. |
Abstract
This project is concerned about improvement of quality management system in company, which is certificated according to norm STN EN ISO 9001:2001. Selected company is Matador Automotive, a.s. Dubnica nad Váhom. Aim of this project is propose corrective steps, which could introduce into the company, for quality improvement reason. This project contains theoretical sources, which are useful for practical parts of this project. Presented theoretical sources are talking about process of quality improvement, way of improvement, sources and tools, which are used for quality improvement. This project describes too, subject of business and other relevant information about selected company Matador Automotive, a.s. Process of quality improvement is performed in development chart, which describes every stages, that we for quality improvement reason have to do. This stages will be in next part of this project practical elaborate. Like a source for elaborate, we will use theoretical part of this project. With combination of management tools we will propose corrective steps, for quality improvement reason. |
Úvod
Súčasný svet sa pomaly dostáva z následkov finančnej krízy, ktorá spôsobila bankroty mnohých firiem a s tým spojené prepúšťanie pracovníkov. Firmy, ktoré chcú v týchto veľmi ťažkých časoch prežiť, musia viac ako kedykoľvek predtým sústrediť svoju pozornosť na potreby svojich zákazníkov. Spokojný zákazník, sa tak stáva kľúčom k spokojnosti celej firmy. Pre zabezpečenie tohto stavu firmám už nestačí len certifikácia systému manažérstva kvality podľa požiadaviek normy STN EN ISO 9001:2009, ale objavuje sa potreba pokračovať v kontinuálnom zlepšovaní zavedeného manažérskeho systému, výkonnosti spoločnosti, efektívnosti, kvality produktu atď. Z toho dôvodu téma tejto diplomovej práce: Návrh súboru opatrení na zlepšenie kvality výroby v spoločnosti Matador Automotive a.s., je veľmi aktuálna, keďže zlepšovanie kvality by malo zabezpečiť upokojenie požiadaviek stále náročnejších zákazníkov a tým zabezpečiť, aby firma bola schopná prežiť tieto náročné časy.
Cieľom diplomovej práce je zlepšiť úroveň kvality v oblasti, ktorú firma považuje za strategicky dôležitú a prvoradú. Danou oblasťou je proces výroby produktu, ktorý je alfou a omegou každej výrobnej spoločnosti. Nekvalita, vyplývajúca z tohto procesu spôsobuje firme veľké finančné škody, ktoré môžu nakoniec spôsobiť závažné problémy. Úlohou bude v sledovanom procese navrhnúť konkrétne nápravné opatrenia, ktoré by zabezpečili zlepšenie ich kvality. Účelom bude znížiť náklady na nezhodné výrobky a tým znížiť firme finančné straty, ktoré musí vynakladať na nezhodnú výrobu. Stanovený cieľ by sa mal dosiahnuť prostredníctvom implementácie manažérskych nástrojov, ktoré sa zaoberajú problematikou zlepšovania kvality. Nástroje, ktoré sa použijú sú podrobne predstavené v teoretickej časti tejto práce. Po oboznámení sa s týmito nástrojmi, práca pokračuje prestavením firmy, kde bola diplomová práca písaná. Vybranou firmou je Matador Automotive a.s. Dubnica nad Váhom. Nasleduje praktická časť diplomovej práce, ktorá sa bude realizovať podľa jednotlivých bodov vývojové diagramu zlepšovania kvality. Postup podľa týchto bodov zabezpečí potrebnú hierarchiu a závislosť, ktorú je pri procese zlepšovania kvality nutné dodržať. Proces zlepšenia bude pozostávať zo ôsmich bodov, ktoré sa následne rozpracujú, za účelom zlepšenia kvality v procese výroby produktu. V prvých bodoch bude prebiehať analýza súčasného stavu, identifikácia slabých miest a určenie relevantných príčin. Nasledovať bude návrh nápravných opatrení, posúdenie a praktické zavedenie vybraných návrhov do prostredia firmy. Vyhodnotenie úspešnosti bude nevyhnutnou spätnou väzbou, ktorá je pri procese zlepšovania kvality veľmi dôležitá.
Teoretické východiská zlepšovania kvality
[1]Vznik intenzívnej konkurencie v globálnom podnikateľskom prostredí vyvolal veľký záujem o skúmanie dôvodov a príčin, prečo niektoré podniky sú mimoriadne úspešné, iné len priemerné a niektoré dokonca zanikajú. Podniky sa obávajú, že na uspokojenie svojich zákazníkov musia vynakladať stále viac finančných prostriedkov. V tejto súvislosti je potrebné rozlišovať medzi nákladmi, ktoré zvyšujú hodnotu produkcie a nákladmi, ktoré žiadnu hodnotu produkcii nepridávajú. V podstate ide o poznanie silných stránok partnerov a vlastného podniku, ktoré sú základným predpokladom prežitia podniku v trhovo orientovanom prostredí. Skutočnosť, že podnik je konkurencieschopný a má potrebnú silu presadiť svoje názory na trhu, vychádza z jeho konkurenčnej výhody, ktorá spôsobuje, že určitá činnosť podniku je v porovnaní s konkurentmi realizovaná lacnejšie, alebo kvalitnejšie v prospech uspokojenia skutočných potrieb zákazníka. Budúcnosť úspešného podniku spočíva predovšetkým v tom, ako podnik dokáže aplikovať množstvo ľudských poznatkov do výrobných postupov tak, aby ich výstupom boli “inteligentné“ produkty.
Organizácie[2], ktoré sa chcú odlíšiť od konkurencie si uvedomujú, že schopnosť uspokojovať potreby zákazníkov nie je realizovaná iba výrobou alebo poskytovaním služby, ale že táto schopnosť vzniká v priebehu celého reprodukčného cyklu. Kvalita musí obsiahnuť všetko to čo vedie k požadovanému výsledku. Týka sa to:
- kvality výrobku ( produktu v hmotnej podobe)
- kvality služby ( produktu v nehmotnej podobe)
- kvality procesov
- kvality zdrojov (stroje a zariadenia, informácií, pracovného prostredia)
- a kvality systému riadenia.
Všetky tieto roviny sa vzájomne podmieňujú a dopĺňajú a preto sa v celom svete šíri rozvíjanie tzv. systému manažérstva kvality, ktoré môžeme charakterizovať ako tú časť celopodnikového manažérstva, ktorá je zameraná na maximálne zabezpečovanie spokojnosti zákazníkov s vynaložením optimálnych nákladov.
Systémy manažérstva kvality[2]
Súbor noriem rady ISO 9000 vrátane normy STN EN ISO 9001:2009 sa zaoberá systémom manažérstva kvality. Normy radu ISO 9000 poskytujú návod k vypracovaniu a uplatneniu efektívneho systému riadenia kvality a manažérstva kvality. Norma STN EN ISO 9001:2009 Systém manažérstva kvality. Požiadavky, umožňuje organizácii stanovením politiky a cieľov kvality, dosiahnuť zhodu s nimi a preukázať túto zhodu iným. Hlavným cieľom tejto normy je podporovať rozvoj efektívneho a prehľadného riadenia spoločnosti. Systém si môžu zaviesť a nechať certifikovať výrobné, obchodné, servisné, montážne, či poradenské a vzdelávacie organizácie zo všetkých oblastí priemyslu a služieb. V súčasnosti sú tieto systémy zavádzané aj vo verejných inštitúciách (úrady, nemocnice, školy). Účinný, efektívny a kvalitne implementovaný systém manažérstva kvality podľa normy STN EN ISO 9001:2009 organizácii garantuje:
- maximálnu spokojnosť a lojalitu zákazníkov a minimalizovať výdaje s tým spojené
- podporovať činnosť neustáleho zlepšovania
- zvýšenie spokojnosti zákazníkov
- zvýšiť kvalitu produktov ( výrobkov a služieb)
- posilniť dôveru a vzťahy medzi organizáciou a zákazníkmi
- zvýšenie prestíže firmy, zlepšenie postavenia na trhu, zvýšenie dôveryhodnosti
- skvalitnenie fungovania (zvýšenie efektivity činnosti)
- sprehľadnenie činností, zavedenie poriadku v organizácii, zníženie výskytu nepodarkov a nezhôd
- vytvorenie základov pre neustále zlepšovanie QMS v organizácii
- zlepšenie funkčnosti a produktivity organizácie
- otvorenie nových príležitostí a udržovanie podielu na trhu.
Spôsoby zlepšovania kvality[3]
Rozpoznávame:
a) strategické prevratné projekty, ktoré vedú k revízii jestvujúcich procesov alebo k zavedeniu nových procesov, zvyčajne realizovaných tímami previazaných funkcií mimo rámec bežných činností;
b) malé postupné a nepretržité zlepšovacie činnosti, vykonávané ľuďmi v rámci jestvujúcich procesov. (Ľudia v organizácii sú najlepším zdrojom myšlienok pre malé zlepšovania, alebo trvalý proces zlepšovania a často sa na ňom podieľajú ako pracovné skupiny. Malé neprestajné činnosti zlepšovania procesu sa majú riadiť, aby sa pochopil ich účinok. Ľuďom v organizácii, ktorí sa do toho zapájajú, má byť udelená právomoc, technická podpora a nevyhnutné zdroje na realizáciu zmien súvisiacich so zlepšením).
Zdroje pre zlepšovanie kvality
Organizácie pre zlepšenie kvality využívajú rôzne zdroje. Tieto zdroje môžeme rozdeliť na hmotné, nehmotné a finančné. Norma STN EN ISO 9004:2000 Systémy manažérstva kvality. Návod na zlepšovanie výkonnosti, predstavuje nasledovné zdroje, ktoré organizácie mô6u využiť pri procese zlepšovania. Zdroje[4] zlepšovania kvality:
- hmotné zdroje ako je zlepšené realizačné a obslužné vybavenie;
- nehmotné zdroje ako je duševné vlastníctvo;
- zdroje a mechanizmy na podporu trvalého inovačného zlepšovania;
- organizačné štruktúry vrátane potrieb manažérstva projektovania a maticového manažérstva;
- manažérstvo informácií a informačná technika;
- zvyšovanie kompetentnosti prostredníctvom školenia, vzdelávania a poučovania;
- využívanie prírodných zdrojov a účinok zdrojov na prostredie.
Proces zlepšovania
Na to aby mohli organizácie zvýšiť efektivitu svojej práce má podľa normy STN EN ISO 9004:2000 proces zlepšovania kvality zahŕňať: Zlepšovanie kvality[3]:
- príčinu zlepšovania: má sa identifikovať problém procesu, vybrať oblasť na zlepšenie a uviesť príčina, prečo sa má na nej pracovať;
- súčasnú situáciu: vyhodnotí sa efektívnosť a účinnosť jestvujúceho procesu. Majú sa zhromaždiť a analyzovať údaje, ktoré odhaľujú, aké druhy problémov sa najčastejšie objavujú. Má sa vybrať konkrétny problém a stanoví sa cieľ zlepšenia;
- identifikáciu možných riešení: majú sa využiť alternatívne riešenia. Má sa vybrať a zaviesť najlepšie riešenie, t. j. také riešenie, ktoré vylúči kľúčové príčiny problémov a zabráni, aby sa problém opakovane nevyskytol;
- vyhodnotenie účinkov: má sa potvrdiť, že problém a jeho kľúčové príčiny sa vylúčili, alebo že sa znížil ich účinok, že riešenie funguje a že sa splnil cieľ zlepšovania;
- zavedenie a štandardizáciu nového riešenia: starý proces sa má nahradiť zlepšeným procesom, aby sa zabránilo opakovanému výskytu problému a jeho kľúčových príčin;
- vyhodnotenie efektívnosti a účinnosti procesu s dokončeným zlepšením: má sa vyhodnotiť efektívnosť a účinnosť projektu zlepšovania.
Nástroje pre riadenie a zlepšovanie kvality
Systém manažérstva kvality využíva viaceré nástroje, za pomoci ktorých dosahuje stanovené ciele. Stanoveným cieľom v diplomovej práci, je zlepšenie kvality výroby vo firme Matador Automotive a.s. Pre dosiahnutie tohto cieľa využijeme nasledovné nástroje:
- PDCA cyklus
- táto metóda popisuje všeobecný nekončiaci proces zlepšovania kvality,
z ktorého filozofie bude vhodné vychádzať.
- Kaizen
- samotný proces zlepšovania kvality budeme realizovať podľa požiadaviek a postupov metódy Kaizen. Táto metóda nám umožní aplikovať malé, postupné zlepšenia, ktoré by mali byť ľahko zrealizovatelné a nemali by firme spôsobiť žiadne veľké finančné zaťaženie.
- Paretová analýza
- túto metódu využijeme za účelom identifikácie slabých miest organizácie.
- Brainstorming
- pre identifikáciu všetkých príčin, ktoré môžu viesť k vzniku nezhodného produktu využijeme práve metódu Brainstormingu.
- Ishikawov diagram
- tento diagram nám v piatich sledovaných skupinách predstaví všetky príčiny, ktoré môžu viesť k vzniku nezhodného produktu (bude zostavený na základe výsledkov Brainstormingu)
V nasledujúcej časti spomínané nástroje, ktoré plánujeme prakticky aplikovať do prostredia firmy predstavíme podrobnejšie. Cieľom tohto bližšieho predstavenia je osvojenie si teoretických vedomostí, ktoré budeme pri ich praktickej aplikácií potrebovať.
PDCA cyklus[5]
PDCA cyklus, nazývaný aj Demingov kruh, predstavuje filozofiu, ktorá napomáha manažmentu v stabilizovaní a zlepšovaní procesov, v dôsledku čoho dochádza k rastu kvality.
Kruh kvality predstavuje nikdy nekončiaci proces zlepšovania, zložený zo 4 krokov:
- 1.krok
- Plánovanie (Plan) – stanovujú sa ciele, spôsoby merania cieľov, identifikujú sa
problémy, ktoré je potrebné riešiť. Pripravujú sa podrobné analýzy a plány aktivít (napr. navrhuje sa mapa procesov),
- 2.krok
- Realizácia (Do) – definuje sa proces súvisiaci s cieľom (problémom), uskutočňuje
sa testovanie plánu, prípadne sa robí nový výskum (získavajú sa údaje), porovnáva sa plán (údaje), identifikujú sa potenciálne problémy a realizujú sa aktivity súvisiace s krokom 1,
- 3.krok
- Hodnotenie – Štúdium (Check – Study) – monitorujú a analyzujú sa uskutočnené
kroky, manažéri sa musia poučiť z dosiahnutých výsledkov. Preverujú sa dosiahnuté výsledky či korešpondujú so stanovenými cieľmi, očakávaniami, plánmi,
- 4.krok
- Nápravné opatrenia (Act) – analyzujú sa dosiahnuté výsledky. V prípade zistenia
rozdielov sa uskutočňujú nápravné opatrenia za účelom zlepšenia procesu a následného zlepšenia kvality celého systému.
Kaizen[6]
Kaizen znamená zlepšovanie produkcie v zameraní na zákazníkov, zlepšovanie všetkých procesov v hodnotovom reťazci podnikových činností, pri súbežnom znižovaní nákladov. Jeho bázou je masová iniciatíva pracovníkov podporovaná efektívnym motivačným systémom. Celková efektívnosť riadenia podniku vychádza práve z dosahovanej produktivity práce, ktorá je sledovaná cez výkony pracovníkov. Vzhľadom k tejto skutočnosti je možné konštatovať, že metóda Kaizen je orientovaná predovšetkým na pracovníkov a ich výkonnosť, pretože pracovníci sú nositeľmi hodnôt v podniku. Cieľom tejto metódy je odstrániť nedostatky, ktoré japonskí manažéri označujú ako „3MU“( Muri-prebytky, Muda-straty, Mura-odchylky). Je to interpretácia troch japonských slov, ktoré symbolizujú tie činnosti, ktorých sa musí podnik bezpodmienečne zbaviť, ak chce, aby sa pri riešení jeho problému dosiahlo rozumnejšie riešenie a vyššia účinnosť. Zásady systému Kaizen:
- Každému zlepšeniu, aj keď by bolo len málo významné, sa musí venovať pozornosť.
- Kaizen je otvorený pre každého. Všetci pracovníci môžu participovať na procese zlepšovania.
- Skôr ako sa nejaké zlepšenie zavedie, musí byť presne analyzované s ohľadom na existujúci stav a možné pozitívne alebo negatívne vplyvy.
- Manažment má dve hlavné úlohy- vytvorenie a udržiavanie štandardov a ich zlepšovanie.
- Zlepšenia hľadať s pomocou pracovných schôdzok tímu. Dôležitá je dobrá príprava a vedenie schôdzky, ako aj výber témy a zabezpečenie presadenia realizácie prijatého riešenia.
- Silná podpora zo strany vedenia podniku. Kaizen je postavený na aktivitách zdola, ale vyžaduje si silnú podporu zhora.
- Vytvorenie organizačných predpokladov pre zlepšenie.
- Motivácia pracovníkov- spoluúčasť na úspechu. Materiálne a finančné ohodnotenie dobrých riešení.
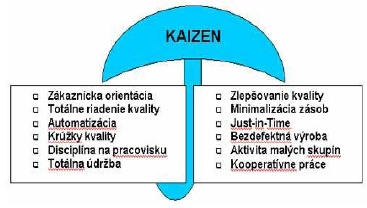
Paretová analýza
Vychádza zo zákonitosti[7], že väčšina následkov má pôvod v relatívne malom počte príčin. Túto zákonitosť objavil a použil pre manažment kvality Dr. Juran. Podľa neho 5 - 20% príčin spôsobuje 80 - 95% výsledných defektov. Inak vyjadrené, odstránením malého počtu systematických príčin sa môže odstrániť väčšina negatívnych javov spôsobujúcich nezhodnosť výrobkov, alebo nespôsobilosť procesov. Paretov diagram vychádza zo zásad Paretovej analýzy (pomerne malá skupina faktorov má za následok väčšinu problémov kvality). Paretov diagram identifikuje a prioritizuje problémy, ktoré je potrebné riešiť. Je dôležitým nástrojom manažérskeho rozhodovania, lebo umožňuje stanoviť priority pri riešení problému s kvalitou tak, aby pri účelnom využití zdrojov bol dosiahnutý maximálny efekt.
Aplikáciou Paretovho princípu je možné stanoviť, že na vznikajúcich problémoch sa rozhodujúcou mierou podieľa len určitá skupina výrobkov z celého výrobného programu, len určití pracovníci z celkového počtu, len niektoré príčiny zo všetkých, ovplyvňujú kvalitu výrobku apod. Toto vymedzenie je veľmi dôležité pre určenie, lokalizáciu problému a jeho efektívne riešenie. Pomocou Paretovho diagramu možno „životne dôležitú menšinu“ identifikovať, čo umožňuje sústrediť pozornosť prednostne na tie činitele, ktoré sa najviac podieľajú na analyzovanom probléme. Správne určenie „životne dôležitej menšiny“ činiteľov je najviac závislé na vierohodnosti spracovaných údajov. Z praktického hľadiska je najvhodnejšie príspevky jednotlivých činiteľov vyjadriť v nákladových položkách.
Postup Paretovej analýzy[8]:
- Zvoliť reálnu situáciu na zlepšovanie.
- Určiť znaky a faktory na pozorovanie a kritériá na ich hodnotenie.
- Stanoviť časové obdobie analýzy.
- Zaistiť prostriedky a pomôcky pre pozorovania, merania, skúšania a pod.
- Zhrnúť získané údaje podľa príčin a zistiť ich početnosť
- Vypracovať diagram a vyhodnotiť rozhodujúce faktory pre 80% nezhôd.
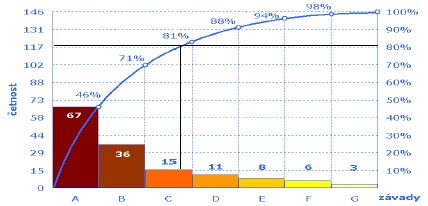
Brainstorming[9]
Brainstorming sa po prvý raz uskutočnil v USA v roku 1938 a jeho názov v preklade do slovenčiny znamená búrka, vytriasanie mozgov“ (brain – mozog, storm – búrka). Tvorca brainstormingu Alex F. Osborn vychádzal z predpokladu, že ľudia mnohé myšlienky a nápady radšej ani nevyslovia, pretože sa boja, že sú nereálne, bláznivé, zlé alebo dokonca smiešne a že nie sú v súlade s tým, čo sa píše v knihách, čo tvrdia autority a čo je konvenčné. Nechcú sa zosmiešniť alebo ukázať, akí sú hlúpi či nepraktickí. Takýto pohľad však tvorivosti neprospieva, a preto treba pri hľadaní nových riešení prekonať sociálne a psychické bariéry, ktoré blokujú vznik netradičných a originálnych nápadov.
Hlavné zásady:
Prvou zásadou brainstormingu je prísne oddelenie tvorby nápadov od ich hodnotenia. Druhou podmienkou je, že kvantita vyvoláva kvalitu – čím viac nápadov, tým väčšia pravdepodobnosť, že sa medzi nimi objaví skutočne skvelá myšlienka. Dôležité je tiež vedieť, že najlepšie nápady sa objavujú spravidla až nakoniec, keď sa všetky konvenčné myšlienky vyčerpali. Tretia zásada vychádza zo synergického efektu, teda z toho, že ak ľudia pracujú spoločne, navzájom sa inšpirujú a pomáhajú si, vyprodukujú viac nápadov, ako keď pracujú individuálne a výsledky ich práce sa spočítavajú. Platnosť týchto zásad Alex F. Osborn a ďalší odborníci empiricky overovali. Podľa výsledkov týchto zistení oddelenie tvorby nápadov od ich produkcie umožnilo vytvoriť až o 90% viac originálnych nápadov ako pri tradičnom spôsobe, keď po vyslovení nápadu ihneď nasleduje jeho posúdenie. Sústredenie na kvantitu nápadov prinieslo o 78% viac originálnych nápadov a synergický efekt – práca v skupine o 70% viac originálnych nápadov, ako pri individuálnej práci členov skupiny a následnom súčte ich nápadov.
Druhy brainstormingu:
V praxi sa využíva niekoľko rôznych variantov brainstormingu. Jedným je napríklad písaný brainstorming, ktorého podstata spočíva v tom, že hárok papiera putuje od jedného účastníka k druhému, pričom každý účastník naň postupne napíše svoj návrh. Pingpongový brainstorming je určený iba dvom účastníkom. Jeden povie návrh, na ktorý druhý účastník reaguje svojím návrhom, potom opäť príde rad na prvého atď. Niektorým účastníkom brainstormingu prekáža, že si problém nemôžu pokojne premyslieť, alebo naštudovať z literatúry. Preto niektorí odborníci zaradili do brainstormingu etapu samoštúdia. Po oboznámení s hlavným problémom pri tomto variante nasleduje etapa samoštúdia a až potom prichádza čas na ďalšie etapy. V praxi sa využíva aj Gordonova metóda. V podstate ide o variant brainstormingu, ktorého cieľom je vytvoriť iba jedno, avšak nové a originálne riešenie problému. Aby sa to dosiahlo, na začiatku nikto okrem vedúceho zasadania presne nevie, aký problém treba vyriešiť. Účastníci ho riešia zoširoka, zo všetkých aspektov, ktoré vedúci postupne zužuje, až sa nakoniec nájde riešenie problému.
Etapy brainstormingu:
- Oboznámenie účastníkov s cieľom stretnutia, problémom a pravidlami
- Tvorba nápadov a riešení
- Prestávka
- Vyhodnotenie návrhov
Bližšie predstavenie jednotlivých etáp je predstavené v nasledujúcej časti:
- Oboznámenie účastníkov s cieľom stretnutia, problémom a pravidlami:
- V tejto etape sa môže uskutočniť aj krátka diskusia o probléme, alebo „mozgová rozcvička“ – netradičné riešenie nejakého menšieho problému.
- Tvorba nápadov a riešení:
- Táto etapa sa zvykne označovať aj ako vlastný brainstorming. V tejto chvíli je mimoriadne dôležité dodržať všetky jeho pravidlá. Všetky nápady sa odporúča písať na tabuľu, alebo veľký papier, aby ich mali pred očami všetci účastníci. Nesmie sa však uvádzať, kto návrh povedal, pretože nejde o ľudí, ale o nápady a riešenia. Účastníci by sa mali hlásiť a pri jednom vystúpení, by mal jeden účastník povedať iba jeden nápad. Optimálny čas tejto etapy sú dve až tri štvrťhodiny s malými prestávkami po každej štvrťhodine.
- Prestávka:
- Podľa charakteru riešeného problému môže trvať niekoľko minút, hodín, ale aj dní. Počas nej sa návrhy „odosobnia“, pričom môžu nastať aj významné zmeny v motivácii účastníkov brainstormingu.
- Vyhodnocovanie návrhov:
- Podstatné je určiť kritériá na hodnotenie návrhov, ktorých by nemalo byť viac ako päť až šesť, lebo inak sa stanú neprehľadné. Nasleduje zaradenie návrhov do istých skupín obdobných návrhov, výber najlepších návrhov na ďalšie rozpracovanie, výber najdivokejších návrhov a úvahy, ako ich možno využiť, zhodnotenie vybraných návrhov. Je dôležité sústrediť sa na to, ako sa nápady dajú uskutočniť, a nie na hľadanie dôvodov, prečo sa uskutočniť nedajú. V tejto etape zohráva kľúčovú úlohu hodnotiace myslenie, dokazovanie, práca s kritériami a ich dôsledkami a pod.
Ishikawov diagram
7Ishikawov diagram je nástroj, ktorý sa používa na grafické zobrazenie príčinnej súvislosti medzi riešeným problémom a jeho príčinami. Pomocou grafického záznamu sa zobrazujú príčiny, ktoré ovplyvňujú výslednú skúmanú vlastnosť, alebo problém. Diagram má tvar kostry ryby. Hlavnú diagonálu predstavuje skúmaná vlastnosť, problém. Priamky smerujúce do hlavnej diagonály predstavujú príčiny, ktoré ovplyvňujú skúmanú vlastnosť, problém. Do nich môžu smerovať ďalšie priamky, ktoré predstavujú podpríčiny nižšej úrovne ovplyvňujúce príčiny vyššej úrovne atď. Hlavné príčiny majú priamy vzťah k skúmanej vlastnosti (následku), každá z podpríčin sa uvádza do vzťahov v poradí podľa úrovne vplyvu k hlavnej príčine. Ako nástroj pre konštrukciu Ishikawovho diagramu je vhodné používať brainstorming alebo brainwriting. Diagram "rybia kosť" je známy diagram „rybacej kosti“ využívaný pre zobrazenie relácie medzi problémami (defektmi) a možnými príčinami ich vzniku. Hlavná os diagramu reprezentuje problém, vetvy stromčeka sú tvorené jednotlivými vplyvmi, ktoré zapríčiňujú problém. Tento diagram by sa mal stať prvým krokom riešenia všetkých problémov, ktoré môžu byť vyvolané viacerými príčinami. Spracovanie je jednoduché a ľahko pochopiteľné, čo vedie k zapojeniu širšieho okruhu pracovníkov a prináša námety, na nové nekonvenčné riešenia. Potrebným predpokladom pre efektívne spracovanie diagramu príčin a následkov je tímová práca s využitím brainstormingu. V prvej fáze tím stanoví hlavné kategórie príčin daného problému.
V prípade problémov s kvalitou výrobku sa často používajú tieto hlavné kategórie:
- materiál;
- zariadenia;
- metódy;
- ľudia;
- prostredie;
Dekompozícia príčin na „príčiny príčin“ by sa mala robiť tak dlho, pokiaľ sa neodhalia všetky koreňové príčiny následku.
Postup vypracovania diagramu[8]:
- Definovanie následku.
- Nakreslenie štruktúry diagramu v tvare rybacej kosti.
- Brainstorming nápadov na príčiny následku.
- Zoskupenie príčin na jednotlivé vetvy a vetvičky diagramu.
- Ukončenie tvorby diagramu vyčerpaním nápadov a ich vhodnou korekciou
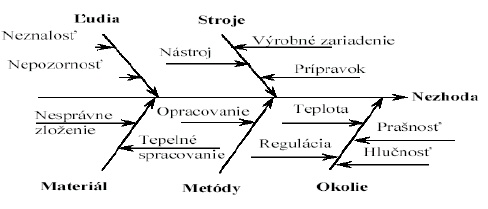
V nasledujúcej časti diplomovej práce predstavíme ďalšie nástroje pre riadenie a zlepšovanie kvality, z ktorých budeme pri návrhu nápravných opatrení vychádzať. Bude sa jednať o nasledovné nástroje a systémy:
- Štatistická prebierka
- Poka Yoke
- Metóda 5S
- Interný audit
- TPM (Totálne produktívna údržba)
Spomínané nástroje a systémy v nasledujúcej časti diplomovej práce bližšie teoreticky predstavíme.
Štatistická prebierka[10]
Štatistická prebierka patrí do skupiny stredne náročných štatistických metód používaných v oblasti riadenia kvality. Využíva sa na vstupnú, medzioperačnú, výstupnú výberovú kontrolu kvality, ak:
- 100% kontrola je príliš nákladná,
- 100% kontrolu nie je možné realizovať (deštruktívne skúšky, kontrola sypkých materiálov, pást, kvapalín, plynov...),
- 100% kontrola nemá 100% účinnosť(kontrola každého kusa je veľmi únavná),
- Náklady spojené s priatím nezhodného produktu nie sú veľké.
Cieľom štatistickej prebierky je rozhodnúť o prijatí, alebo zamietnutí preberanej dodávky výrobkov na základe preberacieho pravidla. Zabraňuje tomu, aby sa do výrobného procesu nedostali suroviny/polotovary nevyhovujúcej kvality, ale aj triedi už dokončené výrobky pred ich odoslaním odberateľovi.
Rozdelenie štatistických prebierok z rôznych hľadísk
- Podľa charakteru sledovaného znaku kvality
- Prebierka porovnávaním, t.j. posúdenie kvality dodávky podľa počtu, alebo podielu dobrých a chybných výrobkov,
- Prebierka meraním, t.j. posúdenie kvality dodávky na základe výberovej charakteristiky, vypočítanej z nameraných dát určenej vlastnosti, alebo rozmeru.
- Podľa počtu výberov, na základe ktorých sa rozhoduje o prijatí, resp. zamietnutí dodávky
- Prebierka jedným výberov,
- Prebierka dvojnásobným výberom,
- Sekvenčná prebierka – postupným výberom.
Správna voľba má vplyv na hospodárnosť prebierky. Z hľadiska prípravy a vlastnej realizácie je najnáročnejšia prebierka postupným výberom, ale z hľadiska počtu kontrolovaných výrobkov je najhospodárnejšia a teda najvhodnejšia aj pre deštruktívne skúšky.
- Podľa riešenia zamietnutej dodávky
- Prebierka nerektifikačná (bez opravy) – neprijatá dodávka sa celá vracia dodávateľovi,
- Prebierka rektifikačná (s opravou) – neprijatá dodávka sa nevracia dodávateľovi, urobí sa kontrola všetkých výrobkov dodávky, nezhodné výrobky sa nahradia zhodnými a ďalej postupuje 100% správna dodávka.
- Podľa početnosti kontroly jednotlivých dávok
- Prebierka s kontrolou každej dávky,
- Prebierka s kontrolou každej k-tej dávky – občasná
- Podľa spôsobu výroby a charakteru predávania konečného produktu
- Prebierka pre hodnotenie úrovne kvality jednotlivých izolovaných dávok,
- Prebierka pre hodnotenie úrovne kvality série dávok toho istého produktu od toho istého dodávateľa, ktoré sú vyrábané za stálych podmienok.
Preberací plán
Vyjadruje jednoznačné pravidlo pre rozhodnutie o prijatí/zamietnutí danej dávky. Preberací plán obsahuje:
- Rozsah výberu (počet náhodne vybraných jednotiek n)
- Preberacie kritérium (Ac Acceptance Number: preberacie číslo, prípustný počet nezhodných jednotiek vo výbere).
Poka Yoke
Je metóda [11]zameraná na včasné odhalenie chýb a následné zabránenie ich následkom, napr. nepodarkom a chybám. Je to pomerne jednoduchý a efektívny systém, v rámci metód budovania štíhleho zariadenia, na redukovanie neúmyselných a nechcených chýb, pôsobených ľudským faktorom. Princípom je inštalácia pomocných prvkov, prípadne úprava pracoviska tak, aby bolo možné vykonávať operáciu „len správne“ t.j. aby nebolo možné robiť chyby.
Najčastejšie ľudské chyby[11]:
- Zábudlivosť, Vynechaná montážna operácia, Nepochopenie, nedorozumenia, Zlá montáž, Chybná identifikácia, Nesprávne upínanie nového kusa, Nedostatok skúseností, Chýbajúci diel, Vedomé ignorovanie štandardov, Zlý diel, Nízka úroveň disciplíny na pracovisku, Spracovanie zlého kusa, Nedbalosť, nepozornosť, Nesprávne prevedenie operácie, Pomalosť, ťažkopádnosť, Nenastavené zariadenie, Chýbajúci dohľad, Uvoľnený, alebo vypadnutý diel, Prekvapenie (neočakávané operácie), Nesprávne pripravené nástroje a prípravky, Sabotáž, Vynechaná montážna operácia, Zábudlivosť.
Poke Yoke[11] odstraňuje tieto nedostatky implementovaním kvality do procesu, eliminovaním omylov, eliminovaním koreňových príčin. Tento systém pomáha vyhľadávať technickými prostriedkami možnú ľudskú chybu, blokovať proces a umožňuje odstránenie chyby v rámci okamžitej spätnej väzby.
Postup [12]:
- Zber a spracovanie údajov z merania a monitorovania produkčných procesov
- Zhromaždenie výsledkov inšpekcie zdrojov chýb
- Identifikácia možných chýb porovnaním výsledkov spracovania údajov, z merania a monitorovania, s výsledkami inšpekcie zdrojov chýb a s programami FMEA
organizácie.
- Štatistická, technická a hodnotová analýza výsledkov identifikácie možných chýb.
- Zostavenie priorít Poka Yoke
- Variantné riešenia priorít Poka Yoke vhodným spôsobom:
- Kontrolná metóda
- Metóda pevnej hodnoty
- Krokovanie pracovných úkonov
- Okamžité zasahovanie
- Poplach
- Technicko-organizačné riešenie optimálneho variantu Poka Yoke. Zavedenie vyriešeného variantu Poka Yoke do konkrétneho produkčného procesu.
- Technicko-ekonomické vyhodnotenie zavedenia riešenia Poka Yoke.
- Štandardizácia úspešnej aplikácie Poka Yoke.
Metóda 5S [13]
Je to súhrn základných krokov pre elimináciu plytvania na pracovisku, základný predpoklad pre zlepšovanie a súčasť niektorých ďalších metodík a konceptov. V hierarchii štíhlej výroby patrí do oblastí štandardizácie procesov a štíhleho pracoviska. Názov symbolizuje začiatočné písmena jednotlivých krokov. Číslo 5 symbolizuje päť krokov metódy. 5S vizualizuje a redukuje plytvanie. Nadvýroba sa označí minimálnou a maximálnou hladinou, chyby sa riešia prostredníctvom zariadení a vizuálneho manažmentu, pohyby – prostredníctvom štandardizovaných techník a zjednodušuje sa hľadanie potrebných vecí a pod.
Metódou 5S možno dosiahnuť zlepšenie a zjednodušenie materiálového toku, rozmiestnenia zariadení, umiestnenia materiálu a zásob. Ďalšími prínosmi sú:
- zlepšenie kvality, produktivity a bezpečnosti;
- lepšia podniková kultúra, postoje ľudí, menšia apatia;
- zlepšené pracovné prostredie.
5S je metóda vhodná pre výrobné aj servisné organizácie.
Princíp metódy 5S
- Separovať – Seiri
- Účelom prvého kroku je oddeliť položky, ktoré na pracovisku musia byť (sú potrebné k vykonaniu operácie na pracovisku a pridávajú hodnotu produktu), majú byť premiestnené (nepoužívané tak často) a musia byť odstránené (vôbec nepoužívané objekty). Pri tomto kroku sa používajú červené kartičky na označenie položiek. Každá položka je zapísaná do karty pracoviska, kde sa určí, či bude položka odstránená z pracoviska, alebo zostáva na pracovisku.
- Systematizovať – Seiton
Cieľom druhého kroku je nájsť miesto pre umiestnenie položiek z prvého kroku. Položky sa môžu priamo označiť do layoutu pracoviska. Dôležité je usporiadať položky na pracovisku tak, aby sa minimalizovali pohyby pracovníkov, skladové plochy a pod., čiže aby sa eliminovalo plytvanie. Pri každej položke sa určí počet, v akom sa bude na danom mieste nachádzať. Pri skrinkách a objektoch, ktoré môžu obsahovať rôzne náradia, prípravky a pod. je vhodné vytvoriť tzv. súpis položiek, čo je v podstate zoznam položiek v objekte. Nové rozmiestnenie položiek na pracovisku je vhodné podporiť štandardom layoutu pracoviska a tiež čiarami na podlahe.
- Stále čistiť – Seisto
V tomto kroku sa pracovisko vyčistí a definujú sa oblasti, ktoré je potrebné v rámci teritória pracoviska čistiť. Teritórium pracoviska sa rozdelí na jednotlivé oblasti, ktorým sa definuje to, čo je potrebné čistiť, kedy sa to bude čistiť, ako často, aké pomôcky sú potrebné pri čistení, kto má čistenie vykonávať a pod. Pri tomto kroku sa využíva formulár štandardu čistého pracoviska, kde sa všetky potrebné informácie zapíšu.
- Štandardizovať – Seiketsu
Štvrtý krok metódy 5S je o štandardizácii všetkých uskutočnených zmien v 1., 2. a 3. kroku. Týmto krokom sa štandardizuje celková starostlivosť o pracovisko. Tu vzniká vizuálny štandard pracoviska, v ktorom sú zachytené všetky aktivity čistenia a rozmiestnenia jednotlivých položiek na pracovisku.
- Sebadisciplinovanosť – Shitsuke
Ak pracovníci nebudú dodržiavať navrhnuté štandardy, tak projekt 5S a zmeny uskutočnené na pracovisku neprispejú k eliminácii plytvania, ale budú plytvanie podporovať. Preto je dôležité, aby ľudia z pracoviska boli vtiahnutí do tímu, ktorý bude implementovať 5S. Aby okrem dobrého slova, bolo navrhnuté 5S na pracovisku dodržiavané, je vhodné ho podporiť tzv. kontrolnou kartou, do ktorej budú vykonané činnosti pracovníci zapisovať a potvrdzovať svojim podpisom.
Prínosy z implementácie metódy 5S
Pracovníci majú všetko na svojom mieste, preberajú si pracovisko medzi zmenami čisté, vedia, čo všetko majú mať na pracovisku a ako majú pracovisko udržiavať čisté.
Ďalej sú to prínosy hlavne:
- zníženie pracovného priestoru o 20 – 40 %;
- zníženie zásob na pracovisku o 80 %;
- zlepšenie kvality o 10 – 20 %;
- skrátenie času na hľadanie o 50 %;
- skrátenie montážnych operácií o 30 %;
- zlepšenie podnikovej kultúry a pod.
- 6S
- Metóda 5S sa rozvíja a dnes je známy aj ďalší krok. Šieste S znamená bezpečnosť. Dôvodom je, aby všetky uskutočnené zlepšenia na pracovisku neohrozovali pracovníkov. Okrem toho, kladie dôraz na prístupnosť a jednoznačnú identifikáciu všetkých bezpečnostných zariadení. Cieľom je predchádzanie nebezpečenstvu pri práci, aby počet pracovných úrazov bol 0.
Interný audit[14]
Auditovanie SMK sa vykonáva na základe požiadaviek normy STN EN ISO 19 011:2003 – Návod na auditovanie systému manažérstva kvality, a/alebo systému environmentálneho manažérstva. Audit podľa tejto normy je definovaný ako systematický, nezávislý a zdokumentovaný proces získavania dôkazov auditu a ich objektívneho vyhodnocovania s cieľom určiť rozsah, v akom sa plnia kritériá auditu.
Interné audity, označované ako audity vykonávané prvou stranou, vykonáva sama organizácia, alebo niekto v jej zastúpení na účely preskúmania manažmentom, alebo na iné interné účely a tieto audity môžu tvoriť základ vyhlásenia o zhode samotnou organizáciou. Vykonávanie interných auditov je nevyhnutné aj z hľadiska prípravy organizácie na certifikačný alebo kontrolný audit, ktorý vykonáva tretia strana tj. nezávislá certifikačná organizácia. Interné audity môžu byť zamerané na auditovanie celého systému, procesu alebo produktu. Pri vykonávaní interných auditov je potrebné dodržiavať základné zásady auditovania tj. etické správanie, čestnú prezentáciu, správnu profesionálnu starostlivosť, nezávislosť a prístup založený na dôkazoch.
Interné audity vo firmách môžu byť zamerané na auditovanie:
- systému,
- procesu,
- produktu.
Pred uskutočnením interných auditov je potrebné posúdiť, aký typ auditu bude firma vykonávať. Dôležitým krokom pred vykonávaním interných auditov je zostavovanie tzv. programu auditu. Program auditu obsahuje všetky činnosti potrebné na plánovanie a organizovanie interného auditu a na zabezpečenie zdrojov na jeho efektívnu a účinnú realizáciu v rámci určeného časového intervalu. Ciele programu auditu môžu vychádzať:
- z priorít manažmentu,
- z potrieb hodnotenia zákazníka,
- z požiadaviek normy,
- z požiadaviek zákazníka.
Zodpovednosť za riadenie programu auditu sa prideľuje kompetentnej osobe, ktorá všeobecne chápe zásady auditu, má kompetencie auditorov a ovláda aplikáciu techník auditu, má zručnosť manažérov chápať činnosti, ktoré sa majú auditovať. Program auditu pripravuje manažér kvality, alebo interný auditor podniku, pričom program auditu schvaľuje manažment podniku. Priebeh auditu podľa STN EN ISO 19011:2003:
Začatie auditu (6.2)
- menovanie vedúceho auditorského tímu,
- stanovenie cieľov auditu, jeho predmetu a kritérií,
- určenie vykonateľnosti auditu,
- výber auditorského tímu,
- vytvorenie úvodného kontaktu s auditovanou organizáciou.
Preskúmanie dokumentov (6.3)
Preskúmanie príslušných dokumentov SMK, vrátane záznamov a určenie ich adekvátnosti s ohľadom na kritéria auditu.
Príprava na činnosti auditu vykonávané na mieste (6.4.)
- príprava plánu auditu,
- pridelenie práce audítorskému tímu,
- príprava pracovných dokumentov.
Auditorské činnosti na mieste (6.5)
- realizácia otváracieho stretnutia,
- komunikácia počas auditu,
- zhromažďovanie a overovanie informácií,
- formulácia zistení z auditu,
- príprava záverov auditu,
- realizácia záverečného stretnutia.
Príprava, schválenie a distribúcia správy z auditu (6.6.)
- príprava správy z auditu,
- schválenie a distribúcia správy z auditu.
Ukončenie auditu (6.7.)
TPM - Totálne produktívna údržba[15]
Autorom systému TPM je Seichi Nakajima, ktorý postupne v 50-tych a 60-tych rokoch študoval systémy pre preventívnu údržbu (Preventive Maintenance) v USA a Európe. Svoje poznatky spracoval v komplexnom návrhu, ktorý dostal pracovný názov Total Productive Maintenance - Totálne produktívna údržba. V roku 1971 tento systém Seichi Nakajima zaviedol do japonských podnikov.
Totálne produktívna údržba (TPM - Total Productive Maintenance) sa orientuje na zapojenie všetkých pracovníkov v dielni do aktivít, ktoré smerujú k minimalizácii prestojov zariadení, minimalizácii nehôd a nepodarkov. Pri TPM ide o prekonanie tradičného delenia ľudí na pracovníkov, ktorí pracujú na danom stroji“ a „pracovníkov, ktorí ho opravujú“. Vychádza sa z toho, že práve pracovník, ktorý obsluhuje stroj, má šancu najskôr zachytiť abnormality v jeho práci a prípadné zdroje budúcich porúch zariadenia. Mottom TPM je: „Ochraňuj si svoj stroj a staraj sa oň vlastnými rukami“. Maximum diagnostických a údržbárskych činností sa teda v TPM prenáša z klasických oddelení údržby priamo na výrobných pracovníkov - výrobné úseky. Začína sa obyčajne so zlepšením poriadku na pracovisku, s čistením strojov a kontrolou ich stavu. Ďalej sa obsluha učí „porozumieť svojmu stroju“, naučiť sa správať ako k svojmu „vlastnému zariadeniu“. Okrem údržbárov a operátorov sa do systému TPM zapájajú aj ďalšie profesie, napríklad z technickej prípravy výroby.
Podstata metódy TPM spočíva v dosahovaní lepšieho využitia strojov a zariadení, skvalitnením práce údržby. V praxi je tento systém založený na princípe včasnej detekcie abnormalít vznikajúcich náhodne prevádzkou stroja a ich odbornom odstraňovaní. Jedným z progresívnych prvkov TPM je presunutie časti zodpovednosti za stroj priamo na obsluhu stroja, založenej na skutočnosti, že práve operátori sú v každodennom kontakte so strojom a preto môžu najrýchlejšie rozpoznať vznikajúcu abnormalitu, ako potenciálny základ vzniku poruchy alebo havárie. Samotná implementácia metódy je však založená na tímovej práci a zmene myslenia personálu. Posun v myslení musí nastať hlavne v optimalizácii vzťahu “človek – stroj”, kedy operátor vystupuje nielen v úlohe samotnej obsluhy stroja, ale aj v úlohe aktívneho spolupracovníka údržby. Je absolútne nevyhnutné, aby bol celý tento systém zastrešený aktívnou podporou zo strany manažmentu projektom zavádzania TPM a spoluprácou technických pracovníkov celej firmy.
Zavádzanie metódy TPM preto prebieha v krokoch, ktoré majú základ v tréningu pracovníkov, zdokonaľovaní ich práce, znalosti stroja a pracoviska. Úvodné kroky TPM sú zamerané na vybudovanie základných predpokladov pre účinné odhaľovanie abnormalít, a to čistotou pracoviska, poriadkom a organizáciou pracoviska. V ďalších krokoch sa pristupuje k budovaniu metód, na základe ktorých operátor preberá určité menej zložité a časovo nenáročné prvky údržby stroja, až po organizáciu pracoviska. Program TPM musí byť podporovaný organizovaním odborných tvorivých stretnutí (workshop) zameraných na odstránenie hlavných príčin znečistenia, zjednodušenia čistenia a inšpekcií stavu strojov a zariadení. Ťažisko programu spočíva v tejto fáze v zvládnutí časti samostatnej údržby operátormi, na strojoch a zariadeniach. Zavádzanie TPM musí vychádzať z dlhodobého projektu, ktorý musí vychádzať z jasne definovaných ročných plánov a ich rozpracovania na dielčie aktivity pre každú prevádzku.
- ↑ KAPITÁNOVÁ, Beáta, TEPLICKÁ, Katarína. 2003. Neustále zlepšovanie kvality benchmarkingovým prístupom. [online].Košice, 2003. 6 s. Grantový projekt VEGA č.1/2574/05. Technická univerzita v Košiciach, Fakulta baníctva, ekológie, riadenia a geotechnológií. [cit. 2010-01-26]. Dostupný z WWW: <http://katedry.fmmi.vsb.cz/639/qmag/mj40-cz.pdf >.
- ↑ 2,0 2,1 IT & T s.r.o. 2007. Avris Consulting : ISO 9001 [online]. Bratislava : 2007 [cit. 2010-02-13]. Dostupný z WWW: <http://www.avrisco.sk/sk/ISO9001?page=10011&conf=62f70ea5d796b2914c7016f68a75f706>.
- ↑ 3,0 3,1 STN EN ISO 9004:2000. Systémy manažérstva kvality. Návod na zlepšovanie výkonnosti: Príloha B: Proces trvalého zlepšovania. Bratislava: Slovenský ústav technickej normalizácie, 2000. 82 s.
- ↑ STN EN ISO 9004:2000. Systémy manažérstva kvality. Návod na zlepšovanie výkonnosti: Manažérstvo zdrojov: Všeobecný návod: Skutočnosti ktoré treba zvážiť. Bratislava: Slovenský ústav technickej normalizácie, 2000. 82 s.
- ↑ KOVÁČOVÁ, Kristína. 2009. Manažment kvality vo vybranom peňažnom ústave : Manažment kvality vo vybranom peňažnom ústave – VÚB banka. [online] Banská Bystrica, 2009. 70 s. Diplomová práca. Bankovní institut vysoká škola Praha, Zahraničná vysoká škola Banská Bystrica. Dostupný z WWW: < http://is.bivs.cz/th/8833/bivs_m/Manazment_kvality_vo_vybranom_penaznom_ustave.txt>.
- ↑ 6,0 6,1 TEPLICKÁ, Katarína. 2007. Kaizen - Kvalita versus 3“MU“. [online]. Košice, 2007. Grantový projekt VEGA č. 1/2574/05. Technická univerzita v Košiciach, Fakulta baníctva, ekológie, riadenia a geotechnológií. Dostupný z WWW: <http://katedry.fmmi.vsb.cz/639/qmag/mj34-cz.htm>.
- ↑ VALDNER, Martin. 2007. Nástroje a metódy v manažmente kvality : Štatistické metódy. [online]. Bratislava, 2007. 16 s. Semestrálna práca. Univerzita Komenského v Bratislave, Fakulta managementu. Dostupný z WWW:< http://www.valdner.com/school_public/FM%20UK%20BA/4roc%20- %20Manazment%20kvality/nastroje%20a%20metody%20MK.doc>.
- ↑ 8,0 8,1 8,2 8,3 ZGODAVOVÁ, Kristína, VIRČÍKOVÁ, Edita, MIZLA, Martin. 2007. Web portál nástrojov, metód a prípadových štúdií manažérstva kvality : Sedem základných spôsobov zlepšovania kvality [online]. Trenčín : 2007 [cit. 2010-02-13]. Dostupný z WWW: <http://www.aqi.tnuni.sk/fileadmin/dokumenty/ Nastroje_a_metody/Poka%20Yoke.pdf>.
- ↑ HRweb. 2007. Rozpútajte búrku nápadov Brainstorming [online]. 2007 [cit. 2010-02-13]. Dostupný z WWW: <http://www.jeneweingroup.com/dokumenty/instore/brainstorming.pdf>.
- ↑ BENKOVÁ, Marta. 2007. Zabezpečovanie kvality procesov. [online]. Košice, 2007. 85 s. Semestrálna práca. Technická univerzita v Košiciach, Fakulta baníctva, ekológie, riadenia a geotechnológií. Dostupné z WWW: <http://files.riadeniekvality.webnode.sk/200000681-b1d31b3c70/ZKP%20-%20SKRIPTA_Benkova.doc>.
- ↑ 11,0 11,1 11,2 CHROMJAKOVÁ, Felicita. 2009. IPA Slovakia : Poka Yoke [online]. žilina : 2009 [cit. 2010-02-13]. Dostupný z WWW: < http://www.ipaslovakia.sk/slovnik_view.aspx?id_s=74 >.
- ↑ ZGODAVOVÁ, Kristína, VIRČÍKOVÁ, Edita, MIZLA, Martin. 2007. Web portál nástrojov, metód a prípadových štúdií manažérstva kvality : Poka Yoke [online]. Trenčín : 2007 [cit. 2010-02-13]. Dostupný z WWW: <http://www.aqi.tnuni.sk/fileadmin/dokumenty/ Nastroje_a_metody/Poka%20Yoke.pdf>.
- ↑ CHROMJAKOVÁ, Felicita. 2009. IPA Slovakia : 5S [online]. žilina : 2009 [cit. 2010-02-13]. Dostupný z WWW: <http://www.ipaslovakia.sk/slovnik_view.aspx?id_s=105>.
- ↑ TEPLICKÁ, Katarína. 2008. Vykonávanie interných auditov systému manažérstva kvality. [online]. Košice, 2008. 11 s. Technická univerzita v Košiciach, Fakulta baníctva, ekológie, riadenia a geotechnológií. Dostupné z WWW: <http://katedry.fmmi.vsb.cz/639/qmag/mj49-cz.pdf>.
- ↑ Rakita Consulting. 2005. Cech majstrov údržby : Systémy údržby [online]. žilina : 2005 [cit. 2010-02-15]. Dostupný z WWW: < http://www.tpm.sk/index.files/Page346.htm>.